SKF partnered with a key customer in Zambia to provide customised lubrication and fire suppression solutions, tailored at enhancing operational safety and efficiency, with the added value of delivering significant sustainability benefits.
“Our customer, a prominent diverse group of companies that offer a wide range of industrial services and solutions, successfully secured a mining contract at one of Zambia’s leading gold mines,” explains Kevin Mills, SKF Regional Manager: KZN & Eastern Cape. “To support this venture, they needed Lincoln P203 8 KG progressive lubrication systems and Muster 38 litre LOP fire suppression systems to be fitted to 21 assorted yellow plant equipment that will be operating on the gold mine.”
As all the machines were sourced from two leading OEMs in Johannesburg, South Africa, the lubrication teams from SKF Johannesburg and the Northwest Province, supported by team Kwa-Zulu Natal, under the supervision of Lee Bismark, Services Manager: Lubrication Systems, installed the lubrication and fire suppression systems on each of the machines at the respective OEM’s East Rand manufacturing facilities. “Faced with a tight deadline from our customer, we successfully met the on-site delivery requirements for their mining contract, bolstering our reputation with them,” affirms Mills.
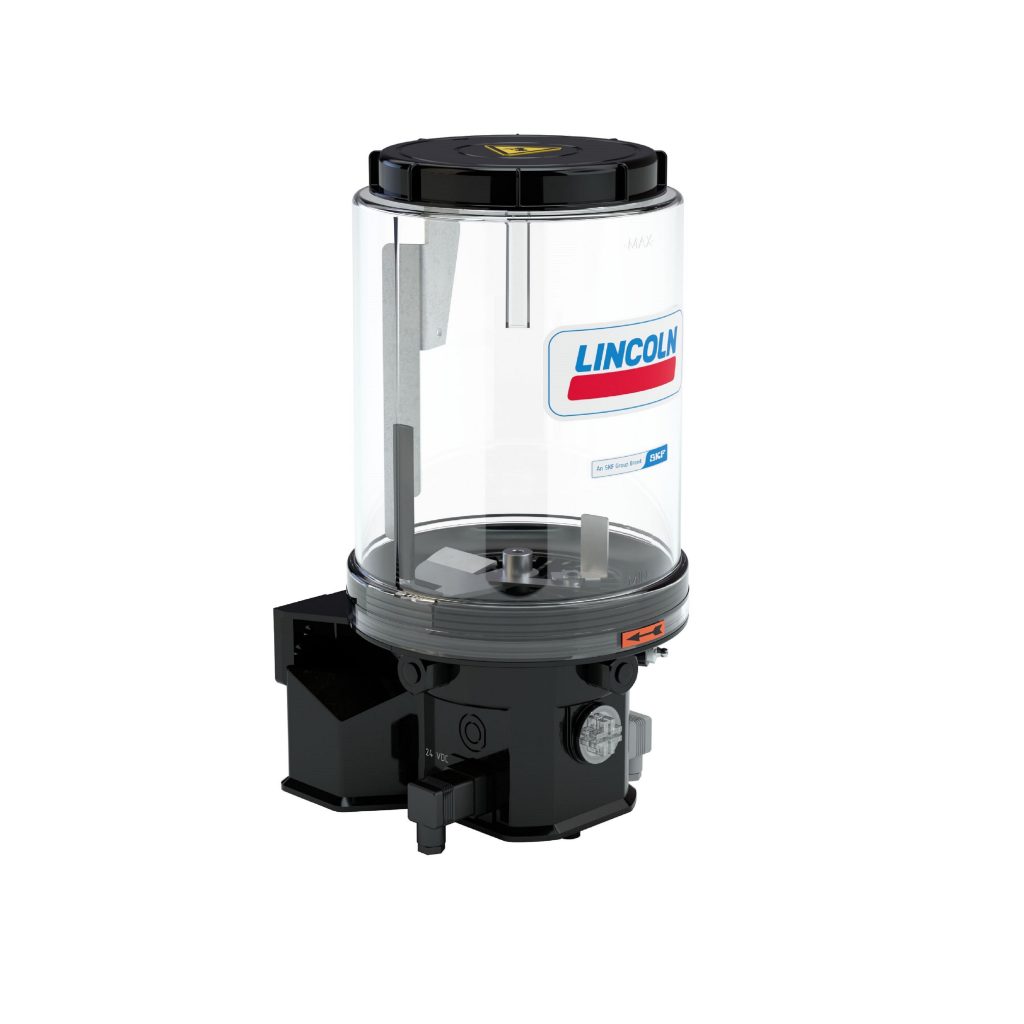
SKF is relentless in the pursuit of excellence, championing sustainability as its guiding principle while actively driving progress toward a greener future. With over a century of experience in bearing and rotating products and cutting-edge technologies, the organisation is committed to the continued development of innovative and intelligent solutions to not only optimise customers’ efficiencies but to also contribute to a greener planet.
Building on this resolve, SKF’s lubrication and fire suppression solutions provide significant sustainability benefits for the customer’s operations in Zambia. This includes a reduction in material consumption and emissions during yellow plant operations. “By optimising both direct and indirect energy usage (from supporting systems), we also contribute to a more energy-efficient operation overall,” adds Mills. “Furthermore, our systems help extend the service life of the equipment while enhancing both machine and operator safety, ensuring a safer working environment as well as reduced downtime and sustainable long-term performance.”
The SKF Zambia team is responsible for ongoing aftersales support to ensure the continued performance and reliability of the machines at the mine, reinforcing the organisation’s commitment to customer satisfaction.
Mills concludes: “The success of this project stands as a testament to the power of collaboration between the entire SKF Africa region, delivering sustainable benefits that will significantly lower operational and ownership costs while helping customers achieve their environmental objectives. “This collaboration is not only a partnership; it exemplifies SKF’s core values of collaboration, curiosity, courage, and care. This model inspires future confidence through sustainable, customer-driven solutions.”
/Ends/