Reducing the risk of catastrophic belt damage.
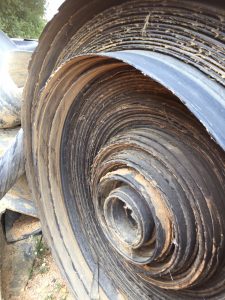
It is estimated that up to 80% of belts that are replaced prematurely are as a result of accidental catastrophic damage. Some regard such damage as impossible to avoid so they use cheap, low-grade ‘sacrificial’ belts. Ironically, the time and money spent on the seemingly endless purchase and changing out of replacement belts, the cost of repairs and the loss of output due to such stoppages is actually far more expensive. Fortunately, there are several ways to significantly reduce the risk of serious, costly damage. As the Dutch philosopher, Desiderius Erasmus, famously said around AD 1500, “Prevention is better than a cure”.
It is not what you expect…….
The biggest single cause of catastrophic conveyor belt damage is trapped foreign objects such as sharp pieces of metal. When lodged in a chute or some other part of the conveyor mechanism, they can puncture the belt cover, penetrate the carcass and cut the belt lengthwise as it is pulled against the object, often over its entire length in a matter of minutes. The first step in reducing the risk and minimize the extent of the damage is to identify where objects are most likely to become trapped and take preventative measures such as installing skirts or screening for example.
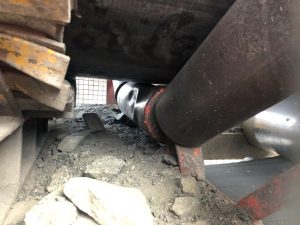
At the same time, areas where spilled materials build up need to be regularly checked and quickly cleared. Apart from increasing the chances of an object becoming trapped, waste build-up is a common cause of damage to idlers and drums, which can cause a lot of collateral belt damage. A significant proportion of belt damage is caused by incorrect installation of auxiliary equipment, damaged, protruding steelwork and components vibrating loose and ultimately becoming detached. The best way to avoid such problems is regular inspection (at least daily) backed up by a preventive maintenance schedule including a policy of rapid replacement of worn or damaged components.
….it is what you inspect.
The importance of daily inspections cannot be over-emphasised. Regular, preventive maintenance, good quality components and a clean working environment all help to prevent damage and extend conveyor belt life. Other factors include making sure that any scrapers are correctly adjusted and that drum linings (where applicable) are in good condition. Belt tracking is also important because a mis-tracked belt can catch on the conveyor framework. Again, having a clean environment is important because mis-tracking is often caused by material build-up on the bottom side of the conveyor belt or drums and pulleys.
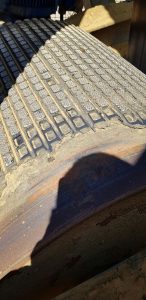
It is not what you expect, it is what you inspect.
The loading point of any conveyor should always be a target for scrutiny because it is often the source of damage. Key factors include making sure that loading is central and at the same speed and direction as belt travel. If necessary, reposition or redesign chutes to reduce the velocity of free-falling material.
Engineered for the task.
Having taken such preventative measures, the risk of serious damage can be substantially reduced even further by fitting a conveyor belt that has been specifically engineered so that it will not be cut, torn or ripped to shreds under the slightest provocation and will run for years as a result. Specialist belts such as Netherlands-based Fenner Dunlop’s UsFlex and Ultra X range, are proven to last up to four or five times longer than conventional multi-ply conveyor belts. This is because they use uniquely designed, very high-quality rubber and fabric plies that, unlike conventional fabrics, allow the transversal (weft) strands to stretch. As the trapped object is pulled through the belt, the strands gather into a bundle that eventually becomes strong enough to stop the belt in its tracks rather than propagate over a much long distance. The design of the fabric also allows the energy created by heavy impact to be dissipated over a much wider area rather than rupture the inner carcass.
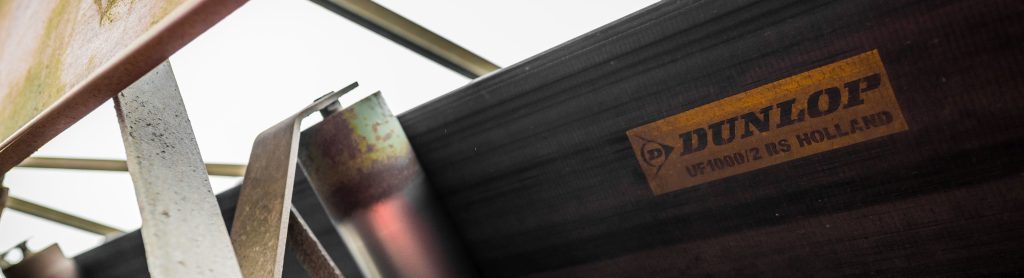
Engineered for the task – up to four or five times longer working life.
Although the initial purchase price may appear high, specialist belts such as the one’s I have mentioned will, over their lifetime, cost substantially less than even the cheapest, thickest lower priced version. Beware, however, of cheap imitations because all the evidence points to them having more than 60% less rip & tear resistance compared to the real thing, which is why they cost much less to make. As they say, price is what you pay but cost is what you actually spend.
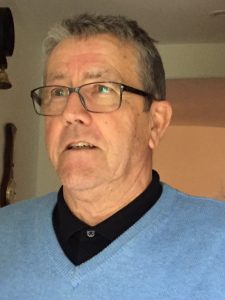
About the author Leslie David :After spending 23 years in logistics management, Leslie David has specialised in conveyor belting for over 17 years. During that time, he has become one of the most published authors on conveyor belt technology in the world.